Warehouse Management Blog
Australian-Made Products in Construction: Better Durability and Reduced Supply Chain Disruptions
Explore the significance of using Australian-made products in construction projects to improve quality, and reduce supply chain agitations and disruptions all the while boosting the local economy.
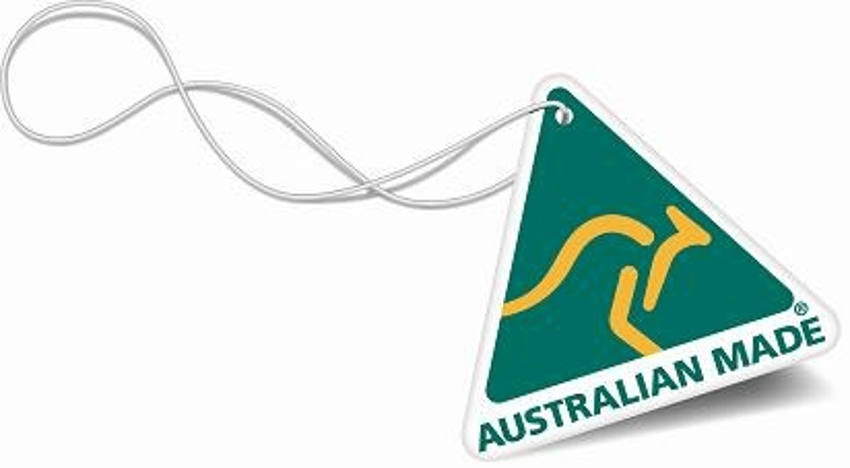
Maximise Your Dealership Design
How you can maximise your dealership design? Looking to create a car dealership that stands out from the rest? Maximizing your dealership design is key to attracting customers and enhancing their overall experience. From the layout of the showroom to the environmental control strategies, every...
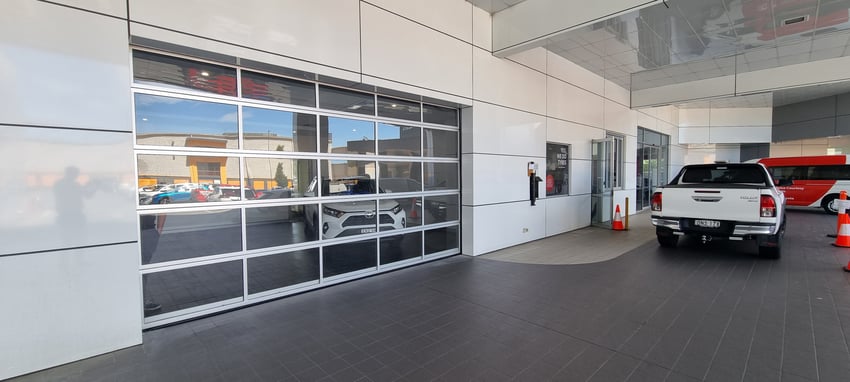
Vehicle Spraying Facilities with Enturi Retractable Sectional Doors
In the dynamic world of manufacturing, the need for innovative solutions to overcome space constraints and operational challenges is ever-present. Recently, Remax Doors successfully tackled a unique challenge for a client operating a vehicle spraying facility.
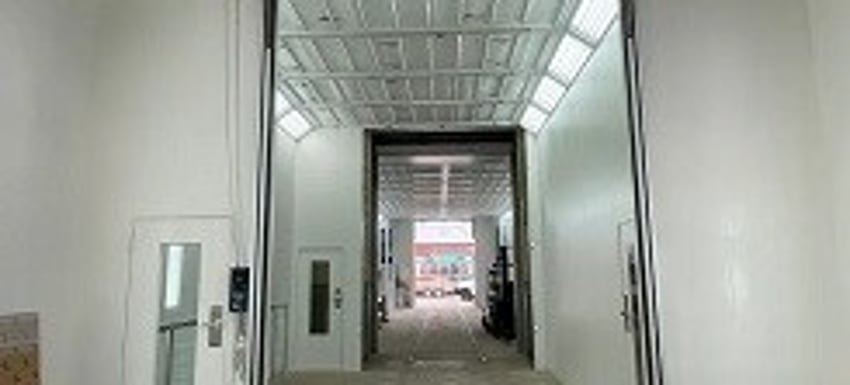
Remax Doors Case Study: Mumford Farms
Mumford Farms, a thriving agricultural business in Victoria, was facing a substantial operational bottleneck in their day-to-day activities. Access to their coolrooms was slow and cumbersome due to manually operated doors.
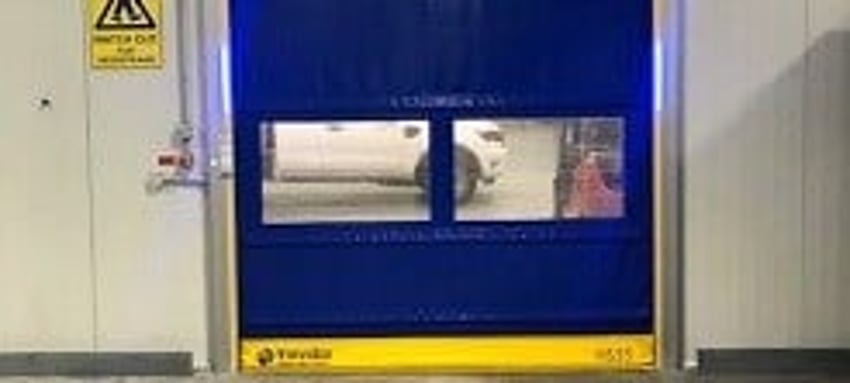
Avoiding Maintenance Issues: Tips for Luxury Car Showrooms
Discover effective tips to avoid common maintenance issues with car showrooms and keep your sectional doors running smoothly for years to come.
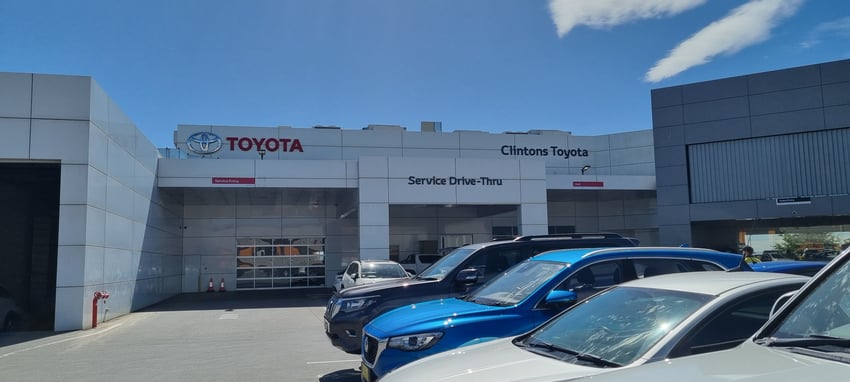
Elevate Your Car Showroom: The Beauty of Foldaway Garage Doors
Transform your garage into a stunning and unique space with luxury garage doors which foldaway into a discrete area above the doorway - where you no longer have to look at the unsightly railings which run along the ceiling, with standard overhead doors . Discover the exceptional craftsmanship and...
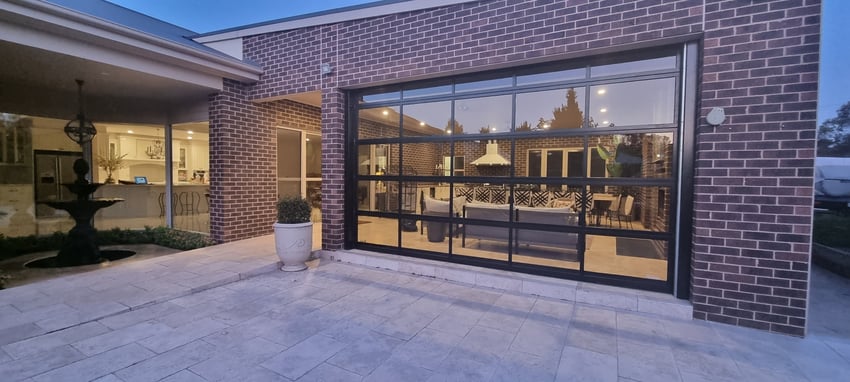
Remax Doors Case Study: Potato Packing Factory Solution
A prominent potato packing factory in South Australia was grappling with a significant problem: birds. Their presence onsite was creating huge problems due to contaminating stock. The current roller doors onsite needed to be upgraded to a more robust solution to combat not only the bird problem but...
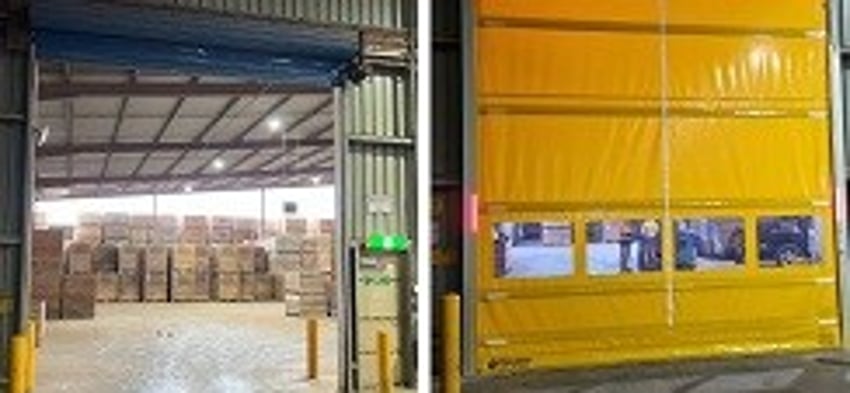
Controlling Dust, Pests, and Contaminants with Rapid Roll Doors
In medium to large scale business operations, maintaining a clean, safe, and efficient environment, these are not just a priority, but a necessity. With a high traffic flow of people and vehicles throughout the facility, keeping out dust, pests and other contaminants can be a challenge. Whether...
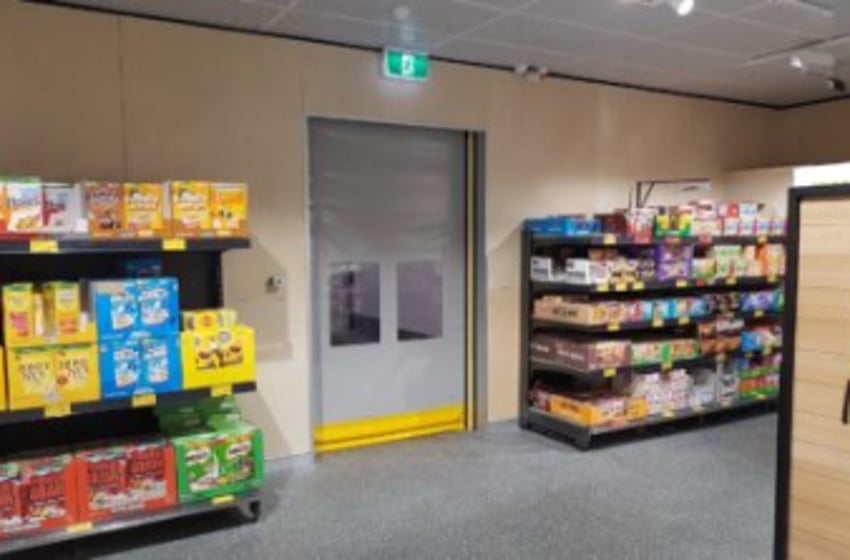
Remax Rapid Roller Doors for Temperature Control
Temperature Control For Warehousing in Winter Temperature control is a crucial aspect of many in may warehouses and large facilities, especially in industries where maintaining a consistent internal environment is key.
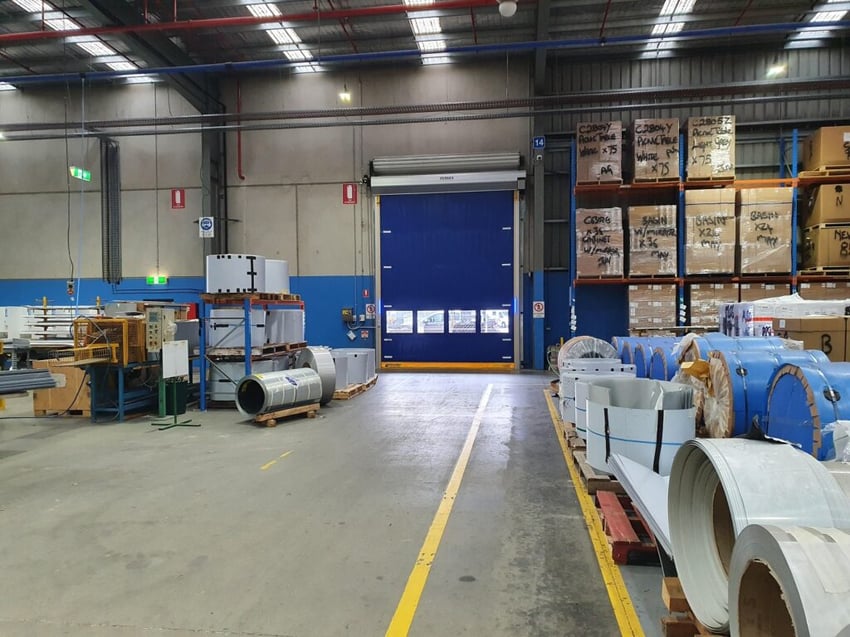
No, you're not seeing things. We have a new logo!
Late last year we had a good look at who we are, who you (our customers) are and the alignment with your needs and the way you prefer to do business. We think our logo update reflects a brand that is a Customer-obsessed, agile to your unique requirements, and genuinely caring about the people we...
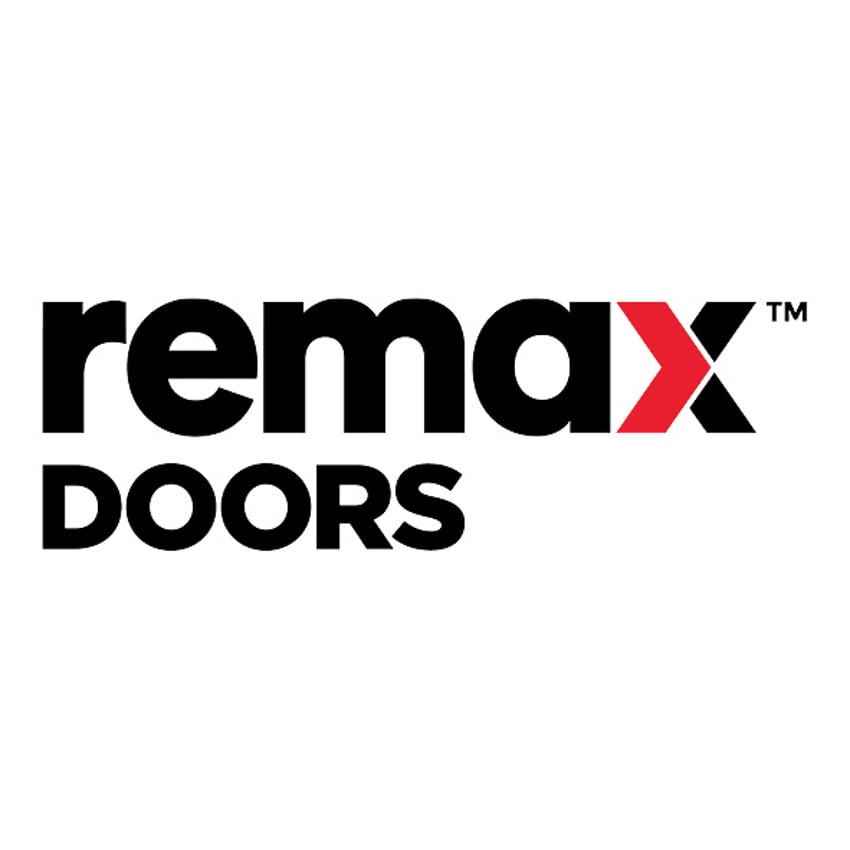